The Importance of Equipment Calibration: Ensuring Accuracy and Reliability
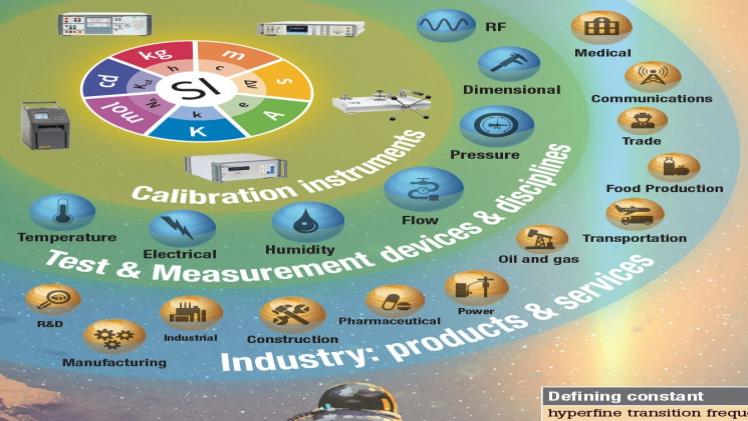
In a world increasingly dominated by precision, equipment calibration emerges as a critical process for several industries, from pharmaceutical laboratories to manufacturing plants. This article explores the importance of this essential service, highlighting how calibration directly impacts product quality, operational safety and regulatory compliance.
What is Calibration?
Calibration is the process of checking and adjusting the accuracy of the outputs of measuring equipment. By comparing a piece of equipment’s readings to a known standard, technicians can adjust its output to reflect accurate values within accepted tolerances. This process is essential to ensure that equipment produces reliable and consistent results, essential for data-based decision making.
Why is Calibration Necessary?
1. Quality Assurance
The quality of products and services directly depends on the accuracy of measurements during the manufacturing process. Poorly calibrated equipment can result in defective products, rework and loss of raw materials, increasing production costs. Regular calibration ensures that production processes remain efficient and that final products meet established quality specifications.
2. Regulatory Compliance
Many industries are subject to strict government regulations that require precision measurement and process control. For example, in the pharmaceutical industry, calibration is mandatory to comply with Good Manufacturing Practices (GMP) standards. Calibration ensures that equipment complies with industry standards and minimizes the risk of legal violations that could result in heavy fines or production disruptions.
3. Operational Security
Well-calibrated equipment is essential for operational safety. In sectors such as chemicals and petrochemicals, where inaccurate measurements can lead to serious accidents, calibration reduces the risk of equipment failures that can cause material and human damage. Keeping instruments calibrated helps prevent dangerous situations and ensure a safe working environment.
4. Cost Savings
Although the calibration process involves initial costs, it is an investment that pays for itself over time. Properly calibrated equipment is more efficient and has a longer lifespan, reducing the need for expensive repairs or early replacement. Additionally, calibration can help identify potential problems before they cause significant damage, avoiding unnecessary expenses and unplanned production downtime.
5. Continuous Improvement
Calibration is an essential part of continuous improvement programs in many companies. By regularly monitoring and adjusting equipment performance, companies can optimize their processes for greater productivity and quality. This not only improves operational efficiency but also strengthens market competitiveness.
See too – Equipment calibration services
How to Implement an Effective Calibration Program?
1. Set Appropriate Calibration Intervals
Calibration frequency should be determined based on usage, importance of the equipment, and regulatory requirements. Equipment used in intense working conditions or that directly impacts the safety and quality of products may require more frequent calibrations.
2. Use Appropriate Standards
Calibration must be performed using nationally or internationally recognized and traceable standards. This ensures that measurements are aligned with global requirements and that results are accepted across all markets.
3. Record and Analyze Data
Keeping detailed records of each calibration and the results obtained allows future analysis and the identification of trends or deviations over time. This data is crucial for adjusting calibration intervals and for internal or external audits.
4. Train your Team
Ensure that technicians responsible for calibration are properly trained and qualified. Technical knowledge and experience are essential to correctly interpret the results and to make precise adjustments to the equipment.
Conclusion
Equipment calibration is not just a technical requirement, but a smart business strategy. Investing in a robust calibration program is investing in the quality, safety and efficiency of production. By ensuring measurement accuracy, companies not only comply with regulations, but also reinforce their commitment to quality and customer satisfaction. Thus, calibration is a key element to sustain and improve operational performance and competitiveness in the global market.